The Art of dépannalisation v cut in PCB Manufacturing
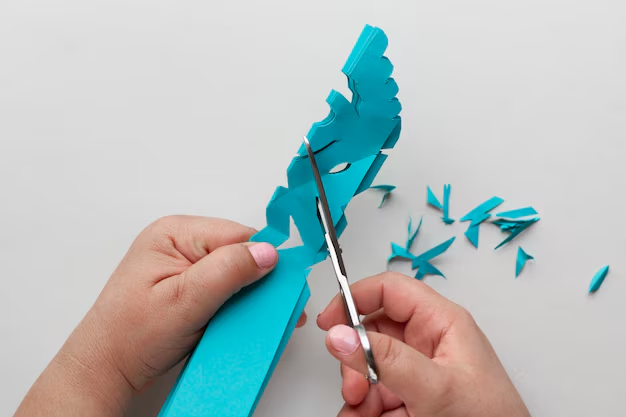
The Art of V-Cut Depanalization in PCB Manufacturing
Depanalization is a critical process in printed circuit board (PCB) manufacturing, enabling the separation of individual boards from a multi-board panel. Among the various depaneling techniques, V-cut depanelization is one of the most commonly used due to its precision, cost-effectiveness, and compatibility with high-volume production. This article delves into the key aspects of V-cut depanelization, its advantages, and how to optimize the process for superior outcomes.
What is V-Cut Depanelization?
V-cut depanelization involves pre-scoring a panelized PCB along the lines where separation will occur. The V-shaped grooves, or “V-cuts,” are etched into both sides of the PCB, reducing material thickness at these lines. During depaneling, the boards are separated along these predefined cuts, ensuring clean edges and minimal stress on components.
Key Components of V-Cut Depanelization
- V-Grooving Process
- A specialized machine cuts V-shaped grooves into the PCB.
- The grooves are typically cut at a 30-45 degree angle.
- Depth is carefully controlled to avoid cutting through the entire board.
- Depaneling Equipment
- Manual Breakers: Simple tools for low-volume production.
- Automated Depaneling Machines: High-speed, precise systems for large-scale manufacturing.
- PCB Design Considerations
- Adequate spacing between components and V-cuts is crucial to prevent damage.
- Uniform groove depth ensures consistent break quality.
Advantages of V-Cut Depanelization
- Cost-Effective
- Requires minimal equipment and setup costs compared to other methods like laser cutting.
- High Throughput
- Ideal for large-scale production with consistent results.
- Minimal Stress on PCBs
- Properly designed V-cuts reduce mechanical stress during separation.
- Compatibility
- Suitable for a wide range of PCB sizes and materials.
Challenges and Solutions
- Risk of Component Damage
- Solution: Maintain adequate clearance between components and V-cuts.
- Inconsistent Groove Depth
- Solution: Use advanced V-grooving machines with precision control.
- Stress Fractures
- Solution: Implement gradual force during the breaking process.
Optimizing the V-Cut Depanelization Process
- Invest in Quality Equipment
- High-precision V-grooving machines ensure uniform cuts.
- Automated depaneling systems improve efficiency and consistency.
- Enhance PCB Design
- Collaborate with designers to incorporate V-cut-friendly layouts.
- Ensure proper component placement and spacing.
- Conduct Thorough Testing
- Test depaneling strength and edge quality to refine the process.
- Employee Training
- Train operators on best practices for handling and separating PCBs.
Applications of V-Cut Depanelization
- Consumer Electronics: Smartphones, tablets, and wearables.
- Automotive Industry: ECUs and infotainment systems.
- Medical Devices: Compact PCBs for portable equipment.
- Telecommunication Equipment: Routers and switches.
Future Trends in V-Cut Depanelization
As PCB designs become increasingly complex and miniaturized, the need for enhanced depanelization techniques grows. Innovations like AI-assisted groove cutting and improved materials are shaping the future of V-cut depanelization.
Conclusion
V-cut depanelization remains a cornerstone of efficient PCB manufacturing. Its cost-effectiveness, scalability, and versatility make it an indispensable process for industries ranging from consumer electronics to automotive applications. By optimizing equipment, design, and operator training, manufacturers can achieve superior results while meeting the demands of modern PCB production.